Plastic extrusion for durable and low-weight components
Plastic extrusion for durable and low-weight components
Blog Article
Checking Out the Various Methods and Technologies Behind Plastic Extrusion
The world of plastic extrusion is a blend of precision, technology, and innovation, pivotal to many markets worldwide. Advanced equipment, computerized controls, and a range of products merge in this intricate process, generating top notch, durable products.
Comprehending the Basics of Plastic Extrusion
The procedure of plastic extrusion, typically hailed as a keystone in the realm of manufacturing, develops the bedrock of this discussion. Fundamentally, plastic extrusion is a high-volume production process in which raw plastic product is melted and created right into a continuous profile. It's a technique widely used for creating products with a constant cross-sectional profile, such as pipelines, window frameworks, and climate stripping. The process starts with feeding plastic materials, usually in the kind of pellets, right into a heated barrel. There, it is blended and warmed until it becomes molten. The liquified plastic is after that compelled through a die, shaping it right into the wanted type as it hardens and cools.
The Duty of Various Materials in Plastic Extrusion
While plastic extrusion is a commonly utilized strategy in production, the materials used in this procedure significantly affect its final result. Various kinds of plastics, such as abdominal muscle, pvc, and polyethylene, each offer distinct residential or commercial properties to the end item. Suppliers must thoroughly think about the properties of the material to enhance the extrusion procedure.
Methods Utilized in the Plastic Extrusion Process
The plastic extrusion process includes different strategies that are vital to its procedure and efficiency (plastic extrusion). The conversation will begin with a simplified explanation of the essentials of plastic extrusion. This will certainly be adhered to by a breakdown of the process thoroughly and an exploration of approaches to improve the performance of the extrusion strategy

Recognizing Plastic Extrusion Basics
In the realm of manufacturing, plastic extrusion stands as a basic procedure, necessary in the manufacturing of a wide variety of daily products. At its core, plastic extrusion involves changing raw plastic product right into a constant profiled shape. This is achieved by melting the plastic, typically in the form of pellets or granules, and compeling it with a shaped die. The resulting item is a lengthy plastic piece, such as a panel, cable, or pipe finish, that keeps the form of the die. This economical technique is extremely versatile, able to create complex forms and fit a wide array of plastic products. Fundamental understanding of these essentials allows for more exploration of the extra elaborate facets of plastic extrusion.
Thorough Extrusion Process Malfunction

Improving Extrusion Strategy Performance
Performance gains in the plastic extrusion procedure can dramatically influence both the top quality of the end product and the general productivity of the procedure. Constant optimization of the extrusion method is critical to keeping an one-upmanship. Strategies that improve performance commonly involve exact control of temperature and stress throughout the process. Modern modern technologies, such as electronic systems and sensing units, have contributed in achieving this control. The usage of premium raw products can decrease waste and enhance result quality. Normal maintenance of extrusion more tips here tools can also lessen downtimes, thus boosting performance. Lastly, adopting lean manufacturing concepts can aid eliminate unneeded actions in the process, promoting performance gains.
How Technology Is Altering the Face of Plastic Extrusion
The introduction of new innovation has actually considerably changed the landscape of plastic extrusion. It has led to the development of innovative extrusion equipment, which has improved the effectiveness and quality of the plastic extrusion process. Additionally, developments in the extrusion procedure have actually additionally been driven by technical innovations, using enhanced abilities and adaptability.
Advanced Extrusion Machinery
Revolutionizing the world of plastic extrusion, progressed machinery imbued with cutting-edge modern technology is ushering in a brand-new period of effectiveness and precision. These equipments, outfitted with ingenious functions like automatic temperature level control systems, ensure optimum conditions for plastic handling, consequently lessening waste and improving product top quality. High-speed extruders, as an example, enhance result rates, while twin-screw extruders offer remarkable mixing capacities, crucial for creating intricate plastic blends. Additionally, digital control systems provide extraordinary accuracy in procedures, decreasing human mistake. These equipments are developed for long life, reducing downtime and maintenance expenses. While these developments are currently remarkable, the constant advancement of technology guarantees also higher jumps forward in the field of plastic extrusion equipment.
Advancements in Extrusion Procedures
Harnessing the power of contemporary technology, plastic extrusion processes are going through a transformative transformation. Advancements such as electronic mathematical control (CNC) systems currently enable more precision and uniformity in the manufacturing of extruded plastic. Automation better boosts efficiency, reducing human error and labor costs. The assimilation of expert system (AI) and equipment learning (ML) algorithms is transforming quality assurance, predicting deviations, and enhancing the total efficiency of extrusion processes. With the development of 3D printing, the plastic extrusion landscape is likewise expanding right into brand-new worlds of possibility. These technological developments are not just enhancing the quality of extruded plastic items however likewise pushing the industry towards a much more sustainable, reliable, and ingenious future.
Real-World Applications of Plastic Extrusion
Plastic extrusion, a effective and functional procedure, locates usage in many real-world applications. The auto sector additionally uses this technology to produce parts like trim and plastic sheet. The stamina and flexibility of plastic extrusion, paired with its cost-effectiveness, make it a crucial procedure throughout numerous sectors, highlighting its prevalent sensible applications.
The Future of Plastic Extrusion: Forecasts and Fads
As we seek to the perspective, it becomes clear that plastic extrusion is poised for significant developments and change. New innovations promise to revolutionize the industry, from smart machinery that maximizes efficiency to lasting products that decrease environmental influence. Automation and robotics are forecasted to play a here are the findings larger role, simplifying manufacturing and making sure constant quality. Eco-friendly alternatives to conventional plastic, such as bioplastics, are also anticipated to get traction. These products not only help to save resources but additionally lessen waste, aligning with international sustainability objectives. Improvements in 3D printing are predicted to open up plastic extrusion brand-new possibilities for customization. These fads indicate a vibrant, developing future for plastic extrusion, driven by technological innovation and a dedication to sustainability.
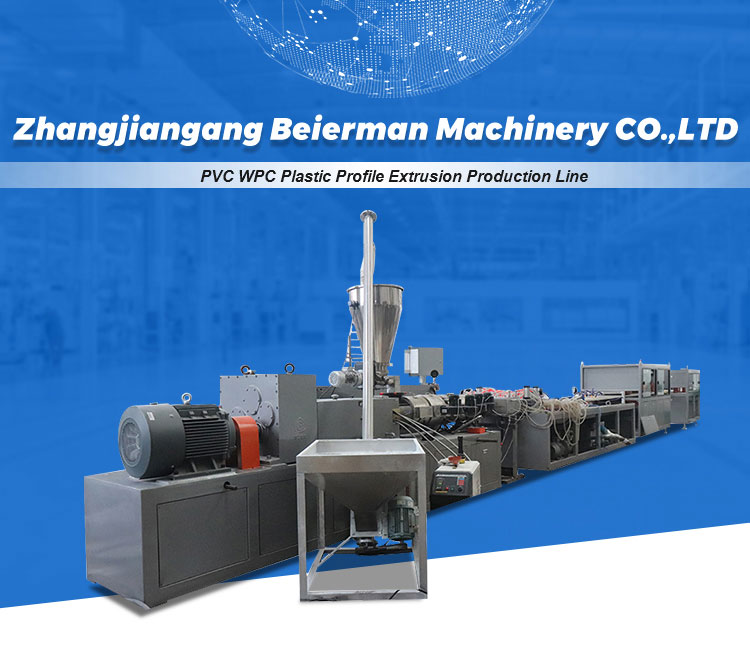
Verdict
To conclude, plastic extrusion is a complex procedure that uses innovative technology and varied products to develop varied items. Technological developments, such as electronic controls, improve the manufacturing procedure and ensure constant results. The market's emphasis on sustainability and smart equipment recommends a promising future. As plastic manufacturing remains to develop, it stays a crucial part of many industries worldwide.
In essence, plastic extrusion is a high-volume manufacturing process in which raw plastic material is thawed and created right into a constant profile.While plastic extrusion is a frequently utilized method in manufacturing, the materials made use of in this procedure considerably influence its final result. At its core, plastic extrusion entails changing raw plastic material into a continual profiled form. It has led to the development of innovative extrusion equipment, which has boosted the performance and high quality of the plastic extrusion process.In conclusion, plastic extrusion is an intricate process that utilizes advanced modern technology and differed materials to create varied products.
Report this page